Modern production of blinds
Our production is one of the most advanced in Central Europe – we purchase material most frequently from Switzerland and France. We have six automated rolling mills, we print product prototypes on a 3D printer, and we check, for example, the accuracy of the cover sheets by means of a laser.
Absolute cleanliness is the basis of our production
In production, we clean up even several times a day and every employee inspects the workplace at the end of their shift. The cleanness of our production amazes everyone who stops by – even our partners from abroad.
Automation
In 2019 we acquired one of the most advanced rolling mills in Europe. This rolling mill was custom-made for us and features built-in rotary four-bed riveting, and using it we make nearly one-third more Z-90 blinds than before. In addition, we work on the principle of smart production control – the data from customers’ orders go directly into machines without us having to copy them by hand.
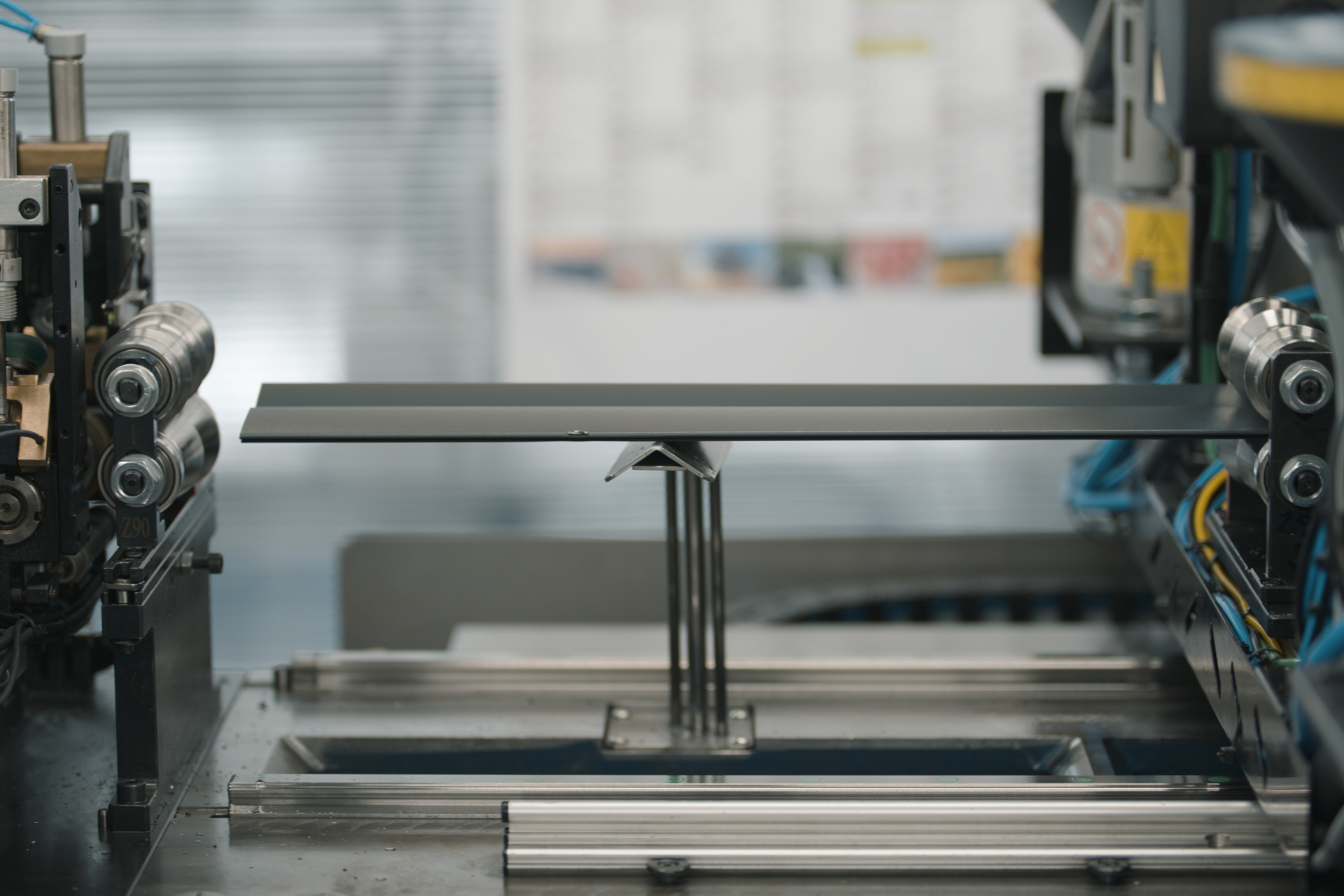
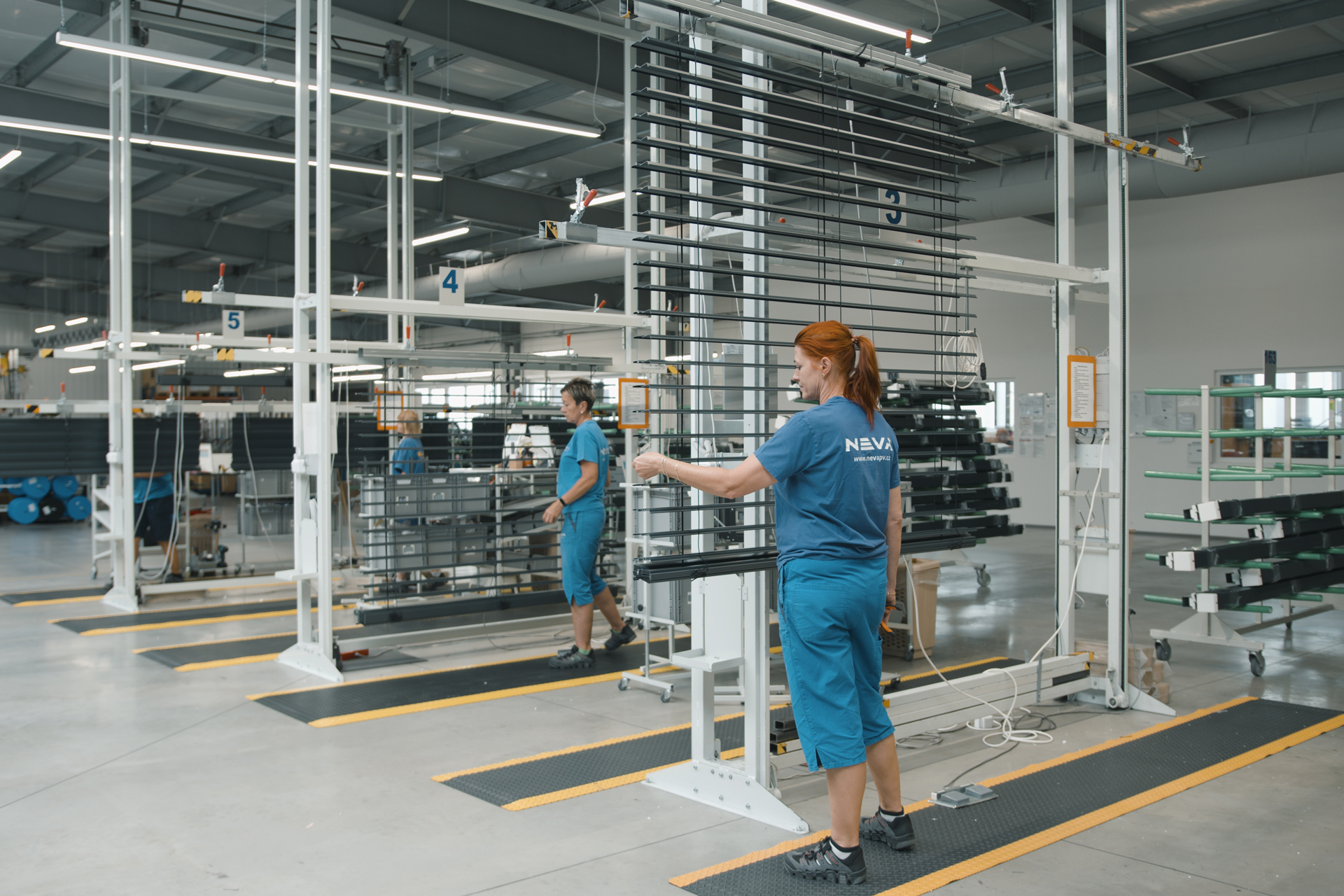
Careful inspection
We inspect blinds several times during production. In addition to the thickness of paint or gloss, we also monitor the functionality of all the parts of the blinds. Once completed, we send the blind for a final inspection and we make all the adjustments already in production, so all it then takes is anchoring on site.
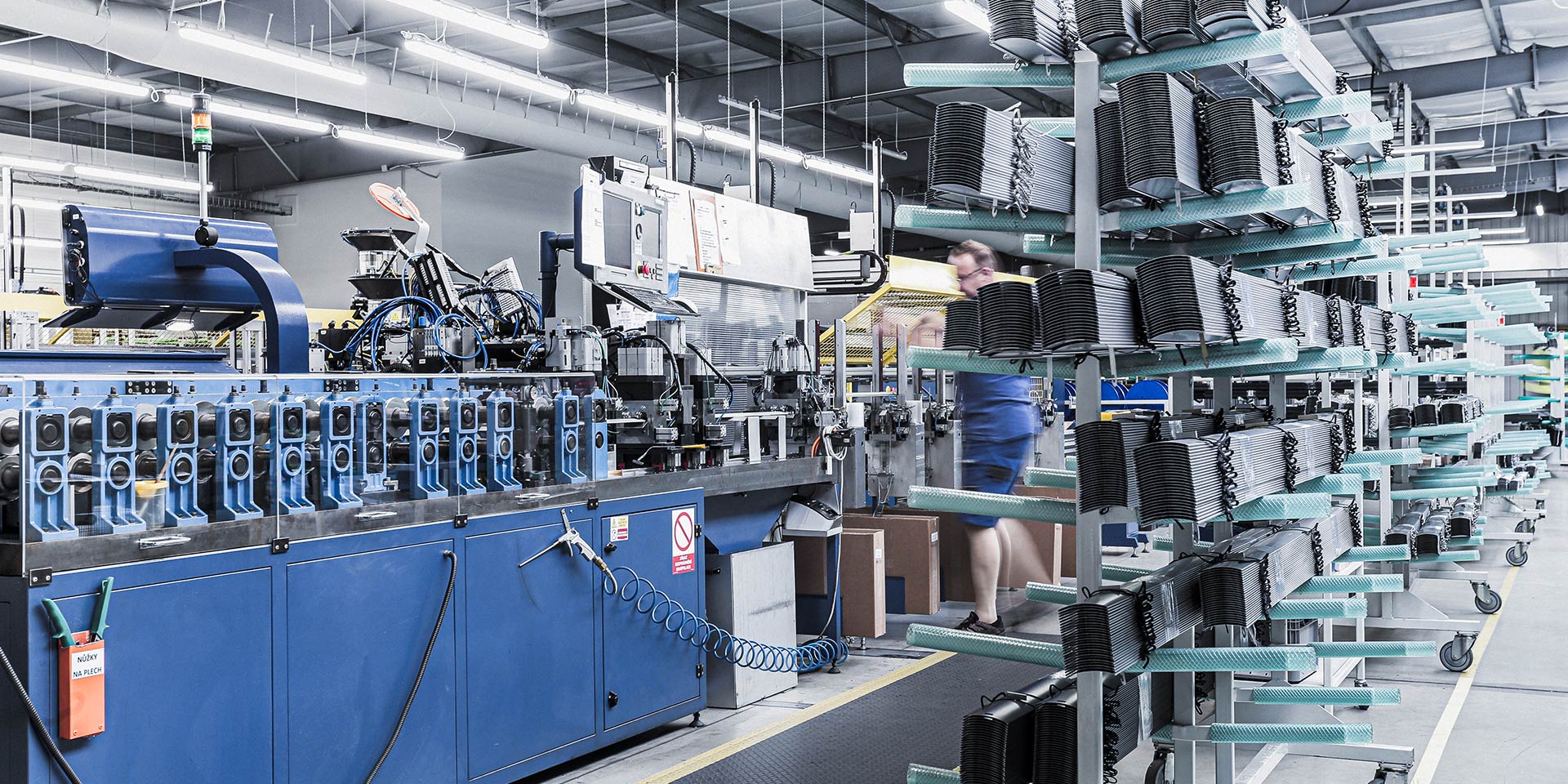
Visit us
Do you want to see our production in person?
Come to see in person how external blinds are produced on first-rate machinery. Write to us and we will arrange a date and take you on a tour of our production hall.
Book a date