Powder coating plant
To have the quality of our blinds fully under control, we built our own coating shop in 2014 for painting components of blinds. We employ the technology of dry powder coating, thanks to which we paint evenly all components, from small aluminium accessories up to 6-metre metal sheets.
We share the capacity of our coating shop with other production companies and we paint components for them as well. We cooperate in this way most often with companies from the closest vicinity, such as from Prostějov, Vyškov, Olomouc, Přerov and Kojetín. If you would like to use the coating shop too, let us know.
Even competitors come to see the cleanness and order in our coating shop.
Following each coating process, we carefully clean the booth to remove residues of the powder paint from it. In order to prevent shades from getting mixed, our painters change their clothes several times a day.
Check out our video from the coating shop
In 2014 we built our own powder coating shop to paint accessories of blinds and textile screens. As a result, we also have short lead times and the quality of coating fully under our control. The head of powder paint shop explains in an interview how the coating shop works, why we keep it perfectly clean and tidy, and how we achieve perfect shades.
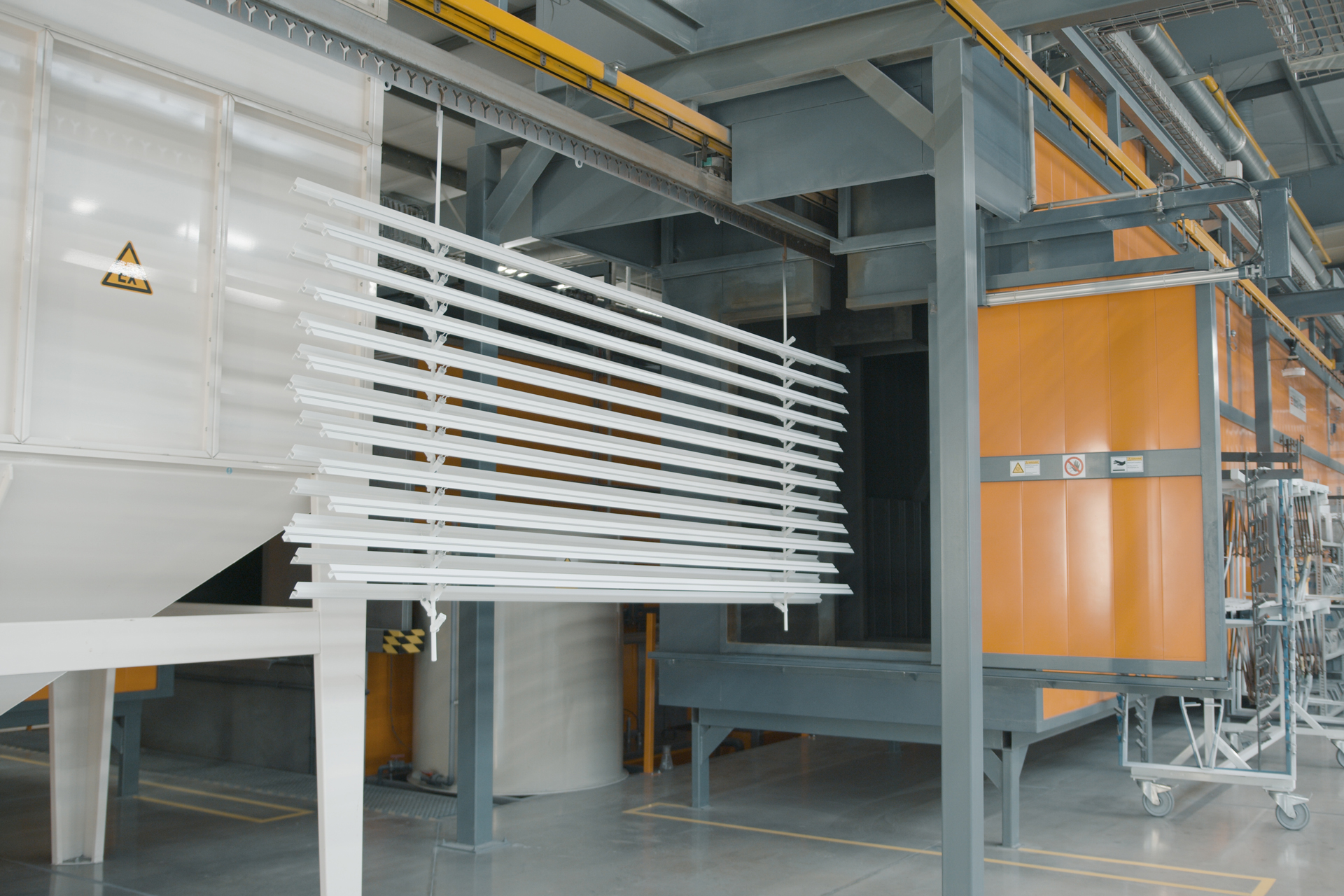
What do the results of our work look like?
We paint products of shading technology, from the smallest components up to aluminium pergolas. You will recognise the careful work of our painters on fences and entrance gates with small motifs or on interior railings.
What does it look like in practice? The step-by-step process of powder coating
We check all guide rails and bottom profiles, clean them on a brushing machine and roughen their surface so that the paint adheres better to the surface. We hang all the parts on a paint hanger, which is part of the semi-automatic enclosed conveyor line.
The parts travel into an automatic spraying line, which consists of two chambers. They spend 30 minutes in both chambers. The first chamber degreases the surface of the parts using an acid cleaner, deoxidises them and rinses them with water. The second chamber rinses the parts with demineralised water so that a titanium conversion nano-layer can form, and cleans them with demineralised water again.
We dry the hangers with components in a direct-fired gas oven at a temperature of up to 150 °C. The hot air circulates around the parts for 30 minutes, perfectly drying the surface, including all the folds.
Dry parts go into the paint booth, where we apply powder paint manually using an electrostatic method. The coating process consists in charging the powder particles with an electric charge and earthing the part being painted. This generates a force that keeps the powder on the part’s surface in a sufficiently thick coat.
Following the application of powder paint, we take the hangers with the parts into the direct-fired gas oven, where the paint hardens at a temperature of up to 200 °C in 20 minutes.
Once the material comes out of the curing oven, we allow it to cool down and then hang it on to handling carts. We leave it here for another 24 hours for the paint to harden.
After the painted parts cool down, we check them one by one, measure the thickness of the coat of paint and the degree of gloss. Afterwards, we carry out destructive tests on test samples that have undergone the same process with the parts painted. If the parts meet stringent quality parameters, we pack everything according to the customer’s requirements.
Do you want to use our coating shop? We paint components of blinds up to the following dimensions.
Material | Height (mm) | Width (mm) | Length (mm) | Weight (kg/pc) |
AL | 1,500 | 1000 | 6,000 | 120 |
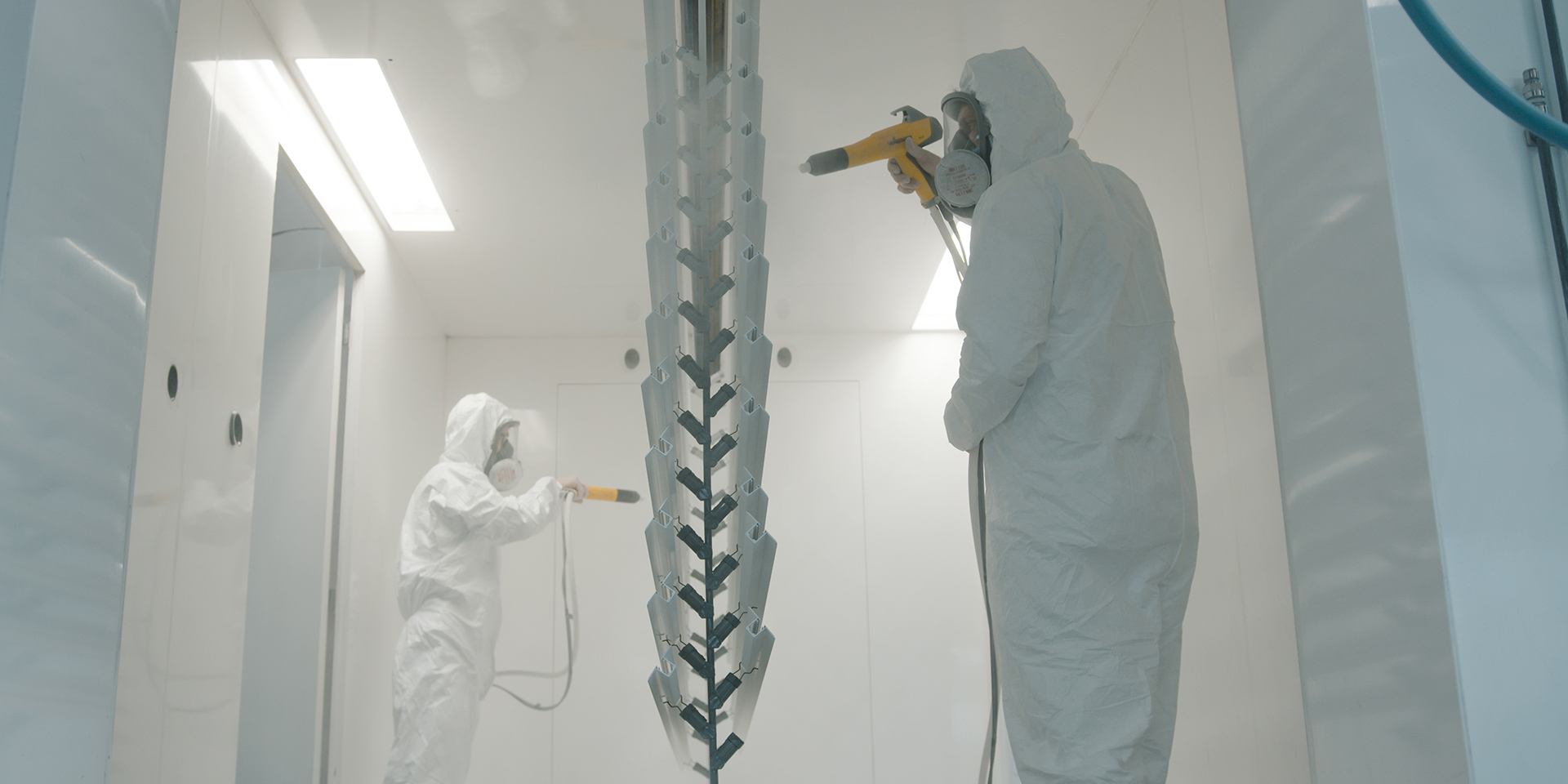
Visit us
Do you want to see our production live?
Come to see in person how external blinds are produced on first-rate machinery. Write to us and we will arrange a date and take you on a tour of our production hall, including the powder coating shop.
Book a date