La fabrication des stores à lamelles extérieurs étape par étape
Dès l’instant où l’un de nos clients nous commande un store à lamelles extérieurs, c’est un processus bien huilé qui se met en œuvre pour créer le produit fini et parfaitement emballé. Lisez cet article pour découvrir comment NEVA fabrique ses stores à lamelles extérieurs.
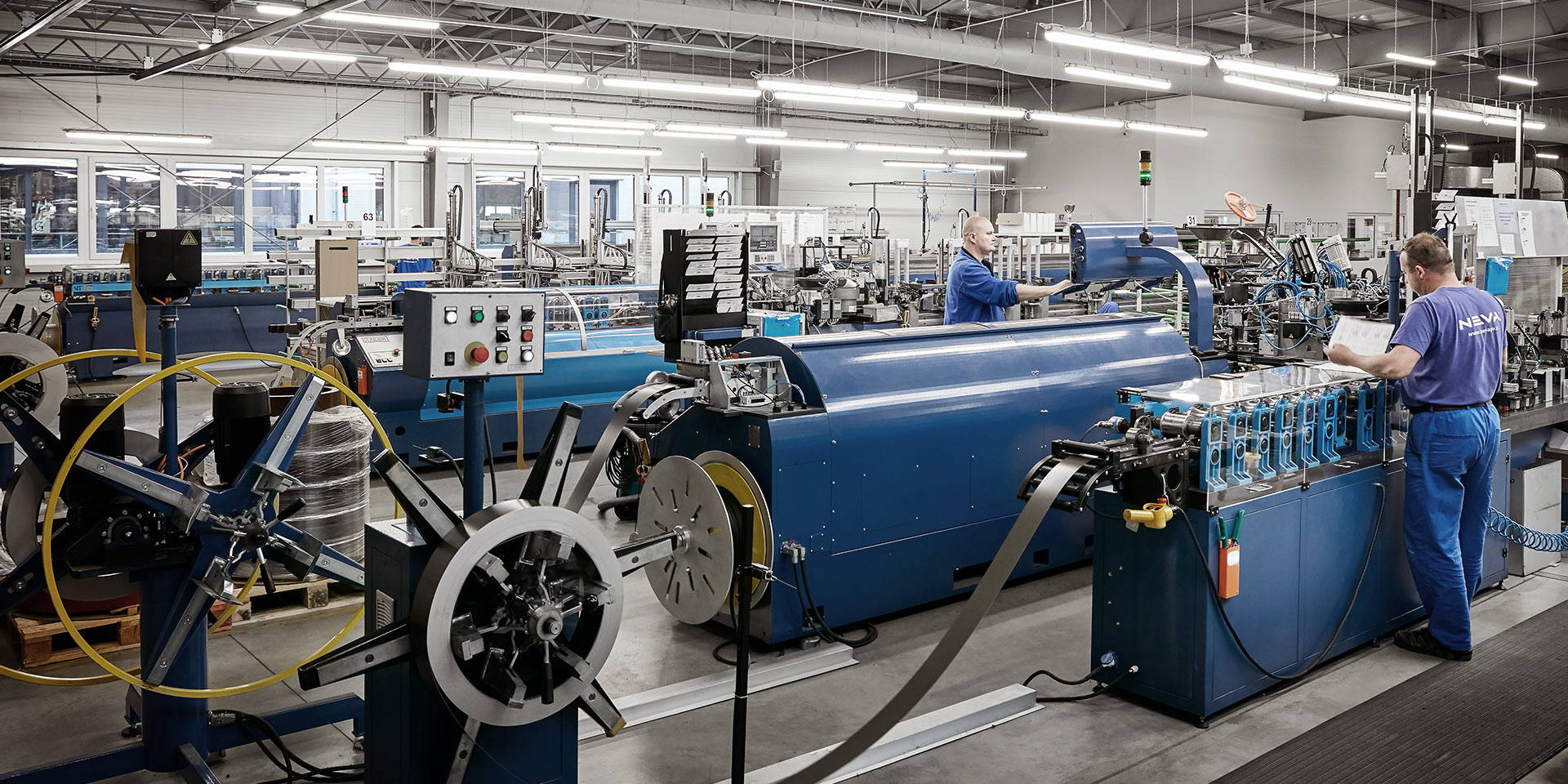
Le laminage permet de donner une forme à nos stores
La fabrication des stores à lamelles extérieurs commence toujours par l’étape du laminage. NEVA dispose de plus de dix lignes de laminage réparties sur 6 laminoirs. Deux d’entre eux sont exclusivement voués à la fabrication des lamelles les plus appréciées, les Z‑90, alors que d’autres peuvent être adaptés en fonction des besoins de production. Nous proposons actuellement 6 types de lamelles de stores extérieurs :
Les dimensions des stores commandées sont envoyées avec le numéro d’identification unique de chaque commande directement depuis le système de commande vers le laminoir. C’est l’opérateur de la machine qui contrôle la couleur commandée. Ce système permet d’éviter les éventuelles erreurs de dimensions ou de type de lames.
Lorsque vous vous placez face au laminoir, vous pouvez voir qu’une extrémité de la machine est alimentée en bande d’aluminium qui circule automatiquement à travers les cylindres de laminage pour que les lamelles sortent à la seconde extrémité, prêtes à être utilisées, c’est-à-dire qu’elles sont alors de bonnes dimensions, déjà dotées des orifices nécessaires au passage du cordon de relevage, avec les crochets nécessaires au passage du cordon d´orientation et avec goupilles de guidage. En dernière étape, la machine enfile automatiquement le cordon d’orientation sur les lamelles et crée ainsi des paquets de lames.
Pendant tout ce temps, les lames restent sous le contrôle de lasers pour que le laminage soit toujours réalisé au millimètre près. Un opérateur contrôle également l’ensemble du processus. Il vérifie la rigidité des lames en effectuant des essais destructifs aléatoires, il règle la machine pour les commandes atypiques et il marque les paquets de lames d’une étiquette pour assurer le bon assemblage de la commande.
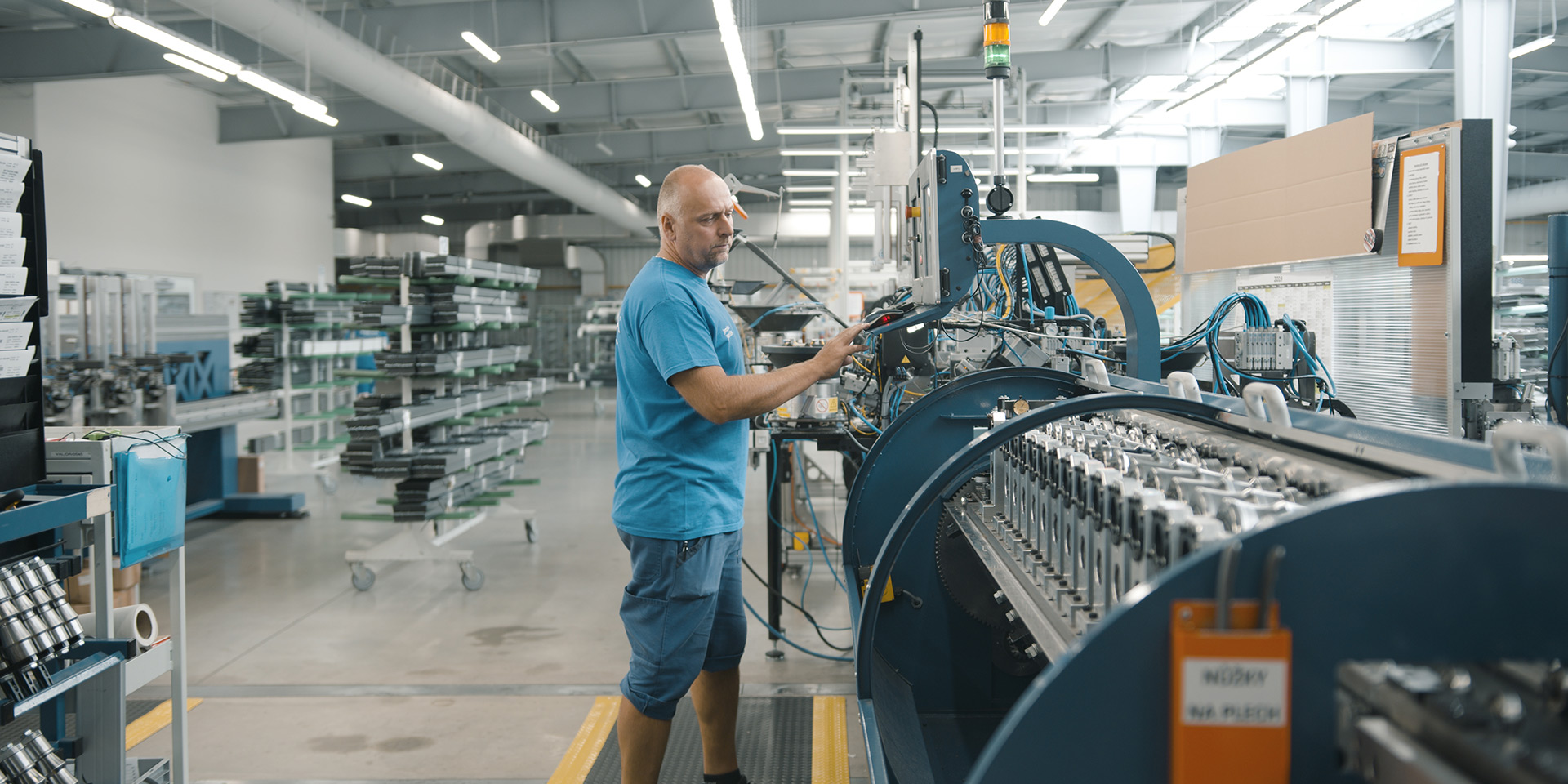
Nous prêtons une attention particulière à la qualité de la peinture. Nous achetons d’ailleurs depuis longtemps nos rouleaux de bandes auprès de l’entreprise suisse Metalcolor qui applique la peinture en plusieurs couches. La haute qualité de nos produits est au cœur de nos préoccupations et c’est justement pour cela que nous sommes totalement satisfaits des produits proposés par Metalcolor.
Des lames parfaitement laminées ne peuvent être obtenues que si le laminoir est parfaitement bien réglé. Nous consacrons donc une attention toute particulière au bon entretien de nos machines. Lorsqu’une équipe de travail commence sa journée et à chaque changement de bande (changement de rouleau, voire changement de couleur), nous fabriquons tout d’abord une lame d’essai. Celle-ci a pour unique fonction de nous permettre de vérifier que le laminoir fonctionne correctement. Si un problème est détecté, nous arrêtons immédiatement la machine pour la contrôler et la régler. Une lame d’essai est bien évidemment aussi fabriquée après chaque opération de maintenance.
Nos opérateurs observent constamment le fonctionnement de la machine pour pouvoir immédiatement en détecter les éventuels problèmes. Ils interviennent ainsi dès qu’un message d’erreur apparaît sur le panneau de contrôle, dès que des copeaux métalliques sont observés ou par exemple que la machine commence à émettre un bruit inhabituel.
Pour éviter tout arrêt technique de notre processus de fabrication, nous veillons à effectuer les opérations de maintenance à intervalles réguliers.
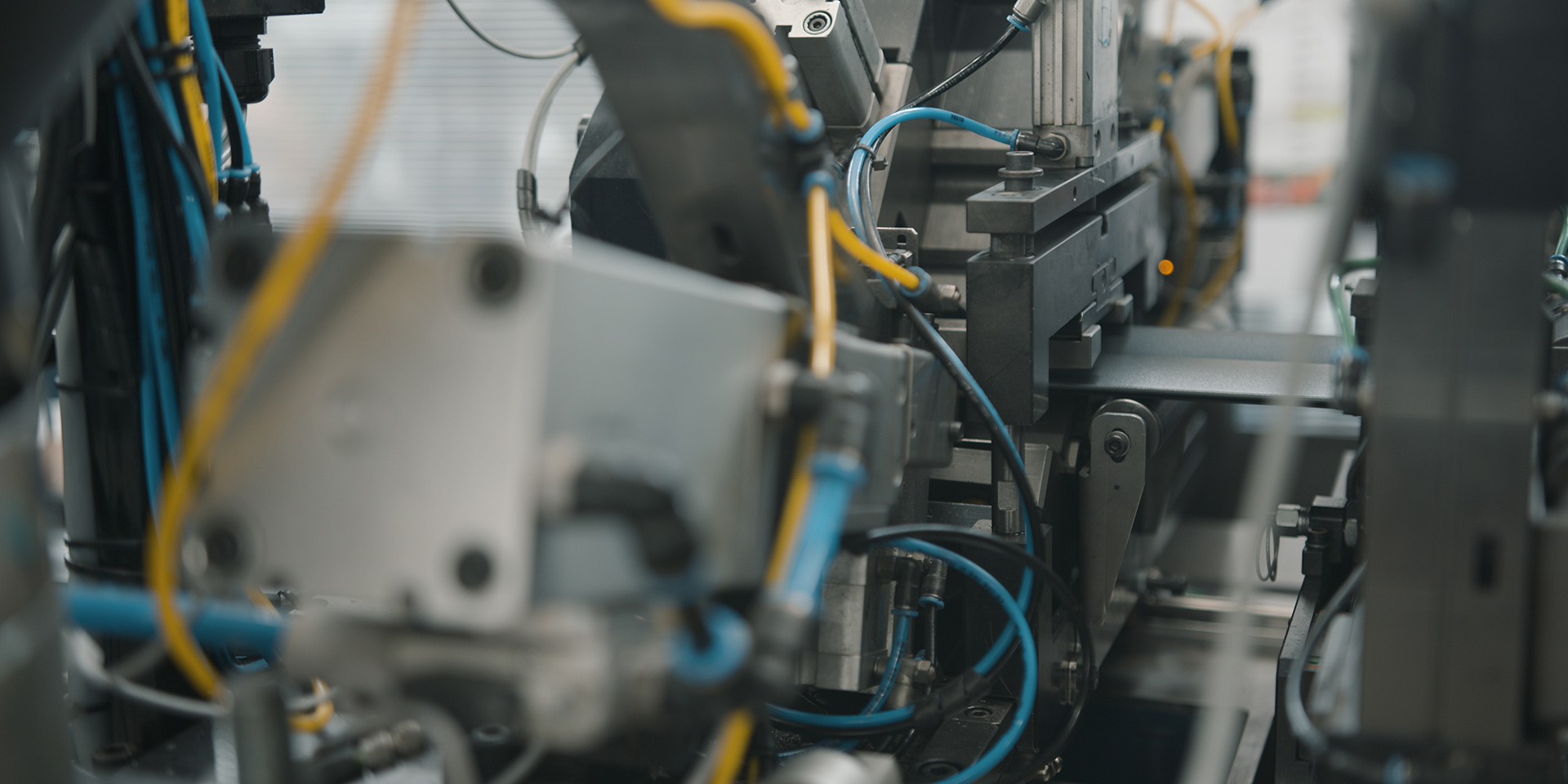
Grâce à notre atelier de peinture, nous pouvons garantir la qualité de la peinture de nos accessoires.
La fabrication de stores nécessite des lamelles, mais aussi des profilés supérieur et inférieur et des éléments de guidage latéraux (c’est-à-dire des câbles ou des coulisses). Les profilés supérieurs sont fournis de façon standard en acier galvanisé et nous les laminons nous-mêmes.
Les profilés supérieur et inférieur sont achetés auprès d’un sous-traitant et nous les peignons dans notre propre atelier de peinture pour qu’ils répondent parfaitement aux exigences de nos clients. Autrefois, nous sous-traitions également les opérations de peinture, mais nous avons finalement choisi de construire notre propre atelier de peinture en poudre en 2014. Cela nous permet de mieux contrôler la qualité des produits finis. Si vous avez envie d’en apprendre plus sur notre atelier de peinture, lisez cet article ou regardez notre entretien avec le chef de notre atelier de peinture.
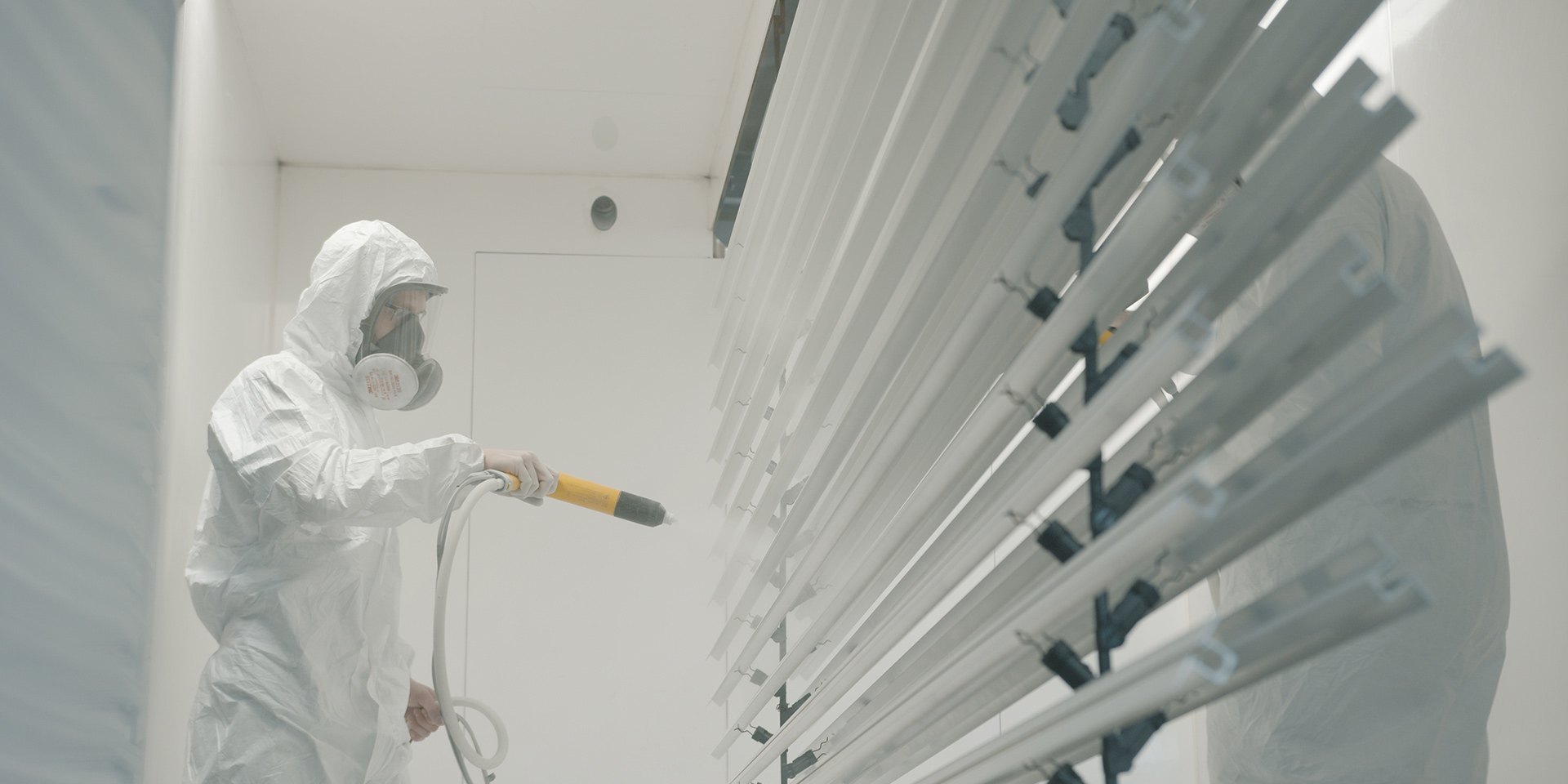
Nos stores sont le plus souvent équipés d’un entraînement électrique
Les profilés supérieurs prennent ensuite la direction d’un autre atelier où ils sont assemblés avec les mécanismes de commande. Les stores à lamelles extérieurs de NEVA peuvent être équipés d’une manivelle ou d’un entraînement à moteur. Nos produits sont le plus souvent dotés d’un moteur Somfy, mais nos clients peuvent aussi par exemple opter pour les marques Elero ou Geiger.
Nos techniciens manipulent jusqu’à 1300 moteurs par semaine.
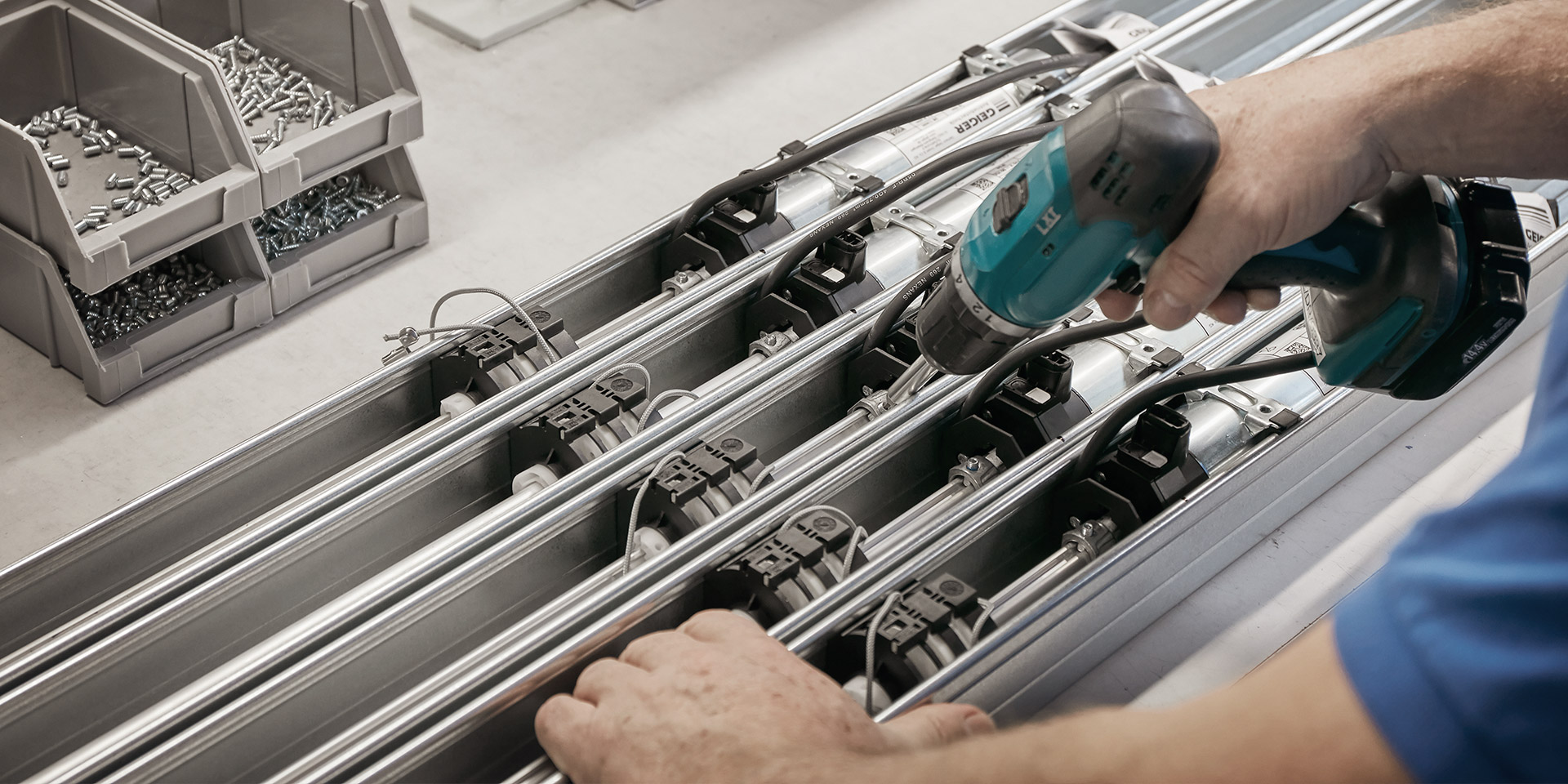
Assemblage, réglage des positions de fin de course et contrôle, tout en un même endroit
Si la commande n’est pas standard, tous les composants du store sont préparés à l’avance pour que les opérateurs disposent de tout ce dont ils ont besoin et qu’ils n’aient pas la peine de chercher ce qu’il leur faut dans l’entrepôt. Les temps d’attente sont ainsi réduits.
Au moment de l’assemblage, nous réunissons tous les éléments du store. Nous commençons par passer le ruban textile à travers les lamelles. Nous réglons ensuite les positions de fin de course haute et basse des moteurs afin que les lamelles aient suffisamment d’espace pour être correctement inclinées. Cela facilite grandement la pose sur le chantier, réduisant ainsi le temps de montage. Sur le poste de contrôle, nous vérifions que le profilé inférieur est parfaitement horizontal et que les dimensions et autres paramètres du store sont parfaitement conformes à ceux indiqués dans la commande. Nous terminons enfin par un dernier contrôle visuel.
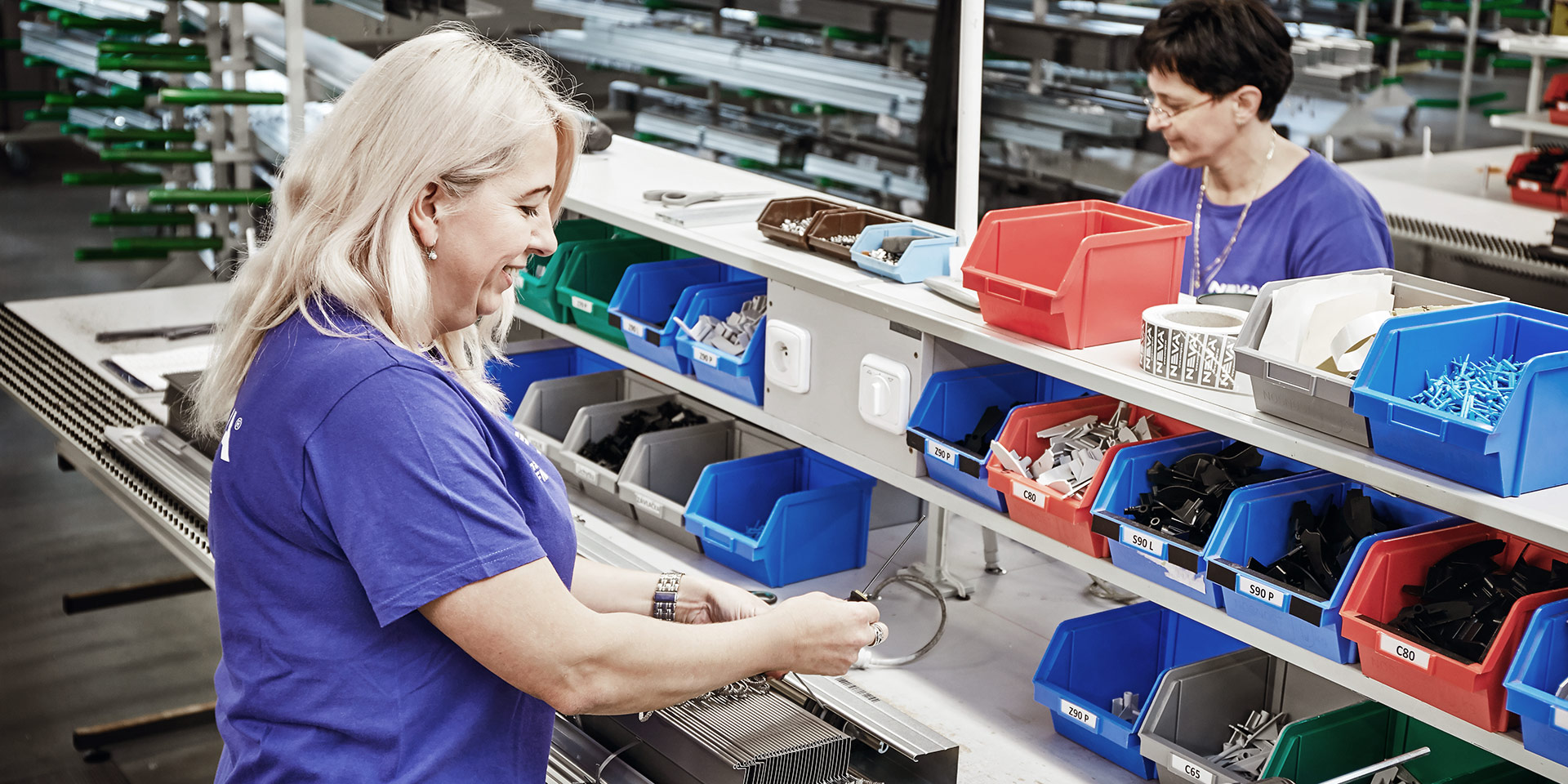
Nous savons parfaitement qui a laminé quel profilé
Notre objectif est de toujours respecter un délai de fabrication de dix jours ouvrés. Chaque étape est essentielle. Aucun retard ne doit être pris. Nous avons donc toujours en stock de grandes quantités de rubans, d’accessoires et de peinture en poudre.
Pour que la fabrication ait lieu de façon aussi efficace que possible, nous avons un coordinateur de production qui veille à ce que tous les stores de mêmes types de lames et de même couleur soient toujours fabriqués en même temps. Les différentes parties des stores sont de plus fabriquées en parallèle et elles sont ainsi réunies au moment de l’assemblage.
Lors de la commande de produits non standards, nous commençons par vérifier que tous les composants sont disponibles dans notre entrepôt ou chez nos fournisseurs afin d’immédiatement pouvoir informer le client de la date de réalisation possible et du prix final.
Dès la saisie de la commande dans notre système, chaque store dispose d’un numéro d’identification et d’un code-barre uniques qui nous permettent de le suivre à chaque étape de la production. Ainsi, chaque opérateur qui intervient sur la commande doit électroniquement confirmer qu’il a bien fait son travail en pipant le code-barre. Nous savons donc exactement quand et par qui chacun des composants a été fabriqué, monté, peint et testé.
Nous veillons particulièrement à la sécurité des produits pendant les étapes d’emballage et d’expédition
Nous livrons les stores NEVA partout dans le monde, c’est-à-dire bien évidemment en République tchèque, mais aussi par exemple en Allemagne, en Scandinavie, en Israël, au Japon et en Australie. Nous veillons pour cela à la qualité de l’emballage. Dès l’étape d’assemblage du profilé supérieur et des lamelles, nous ajoutons des cubes de protection en polystyrène pour éviter que les pièces ne s’usent les unes aux autres, nous protégeons aussi les extrémités des lames et les goupilles de guidage avec du polystyrène, et le cordon d’orientation est emballé dans un film pour lui éviter de s’arracher pendant le transport.
Si nous nous chargeons nous-mêmes du transport, les stores sont tout simplement emballés dans du papier bulle et dans un film étirable, ce qui nous permet d’être plus respectueux de l’environnement, car la quantité de déchets est moins importante, mais aussi de faciliter le travail des poseurs qui n’ont pas à se charger de manipuler de grandes quantités d’emballages. Nos chauffeurs savent exactement comment manipuler nos produits.
Lorsqu’au contraire, une commande est prise en charge par un transporteur externe, nous emballons encore le store dans une boîte en carton. Grâce à notre machine de fabrication des cartons Panotec, nous pouvons créer des cartons dont les dimensions correspondent parfaitement à chacun des produits pour qu’ils ne s’abîment pas pendant le transport. Le nombre de réclamations dues au transport a d’ailleurs largement diminué depuis que nous avons investi dans cette machine.
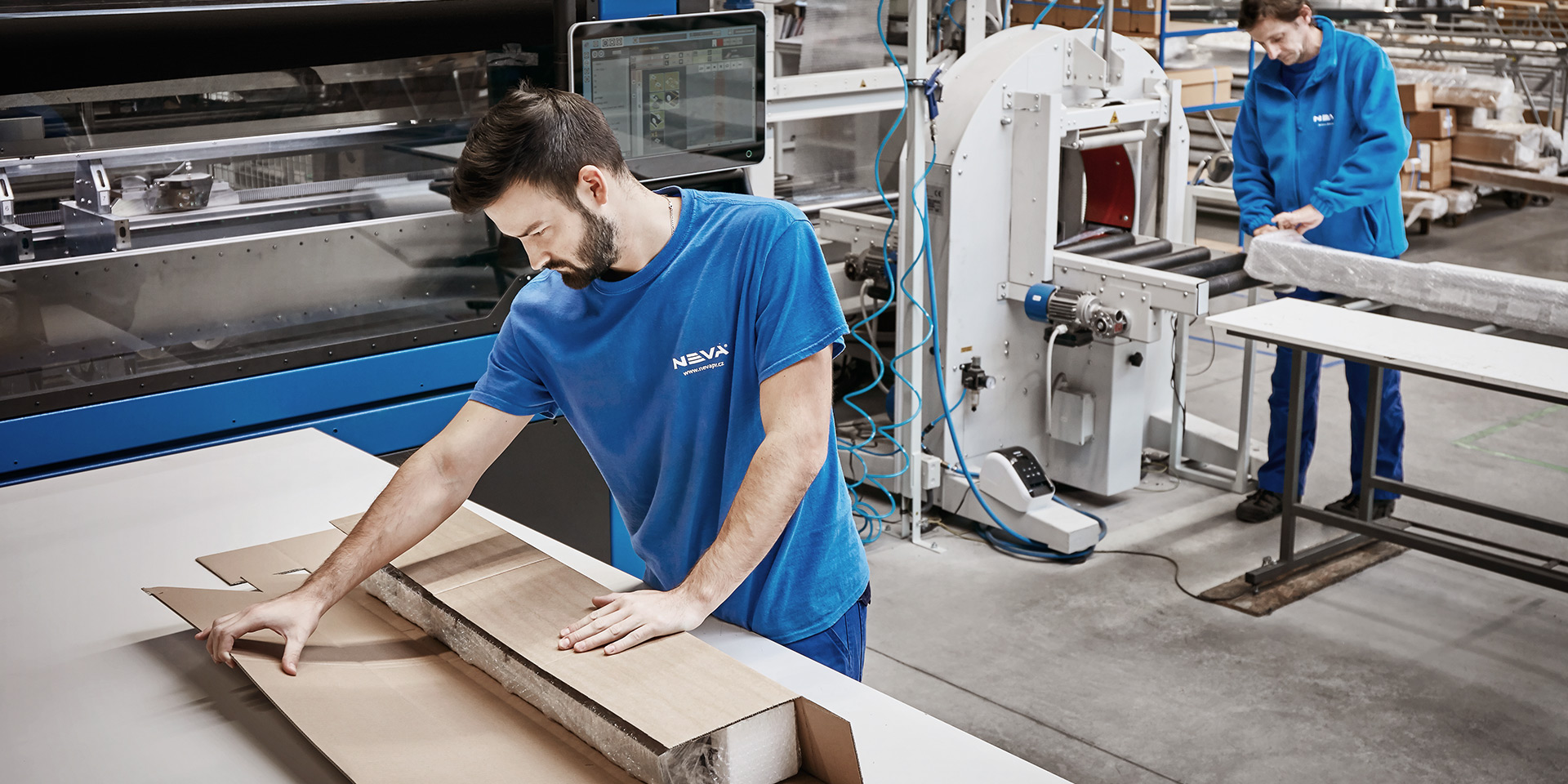
Dans le cas du transport aérien ou maritime, les stores sont déposés dans des boîtes en bois que nous fabriquons également dans notre propre atelier. L’objectif est toujours de garantir une protection maximale contre les dommages.
Si vous avez envie de découvrir notre site de production, il vous suffit de nous le demander. Nous nous ferons un plaisir de nous mettre d’accord sur une date afin de vous présenter l’ensemble du processus de fabrication.